
Initial Research
What does the chair industry look like today?
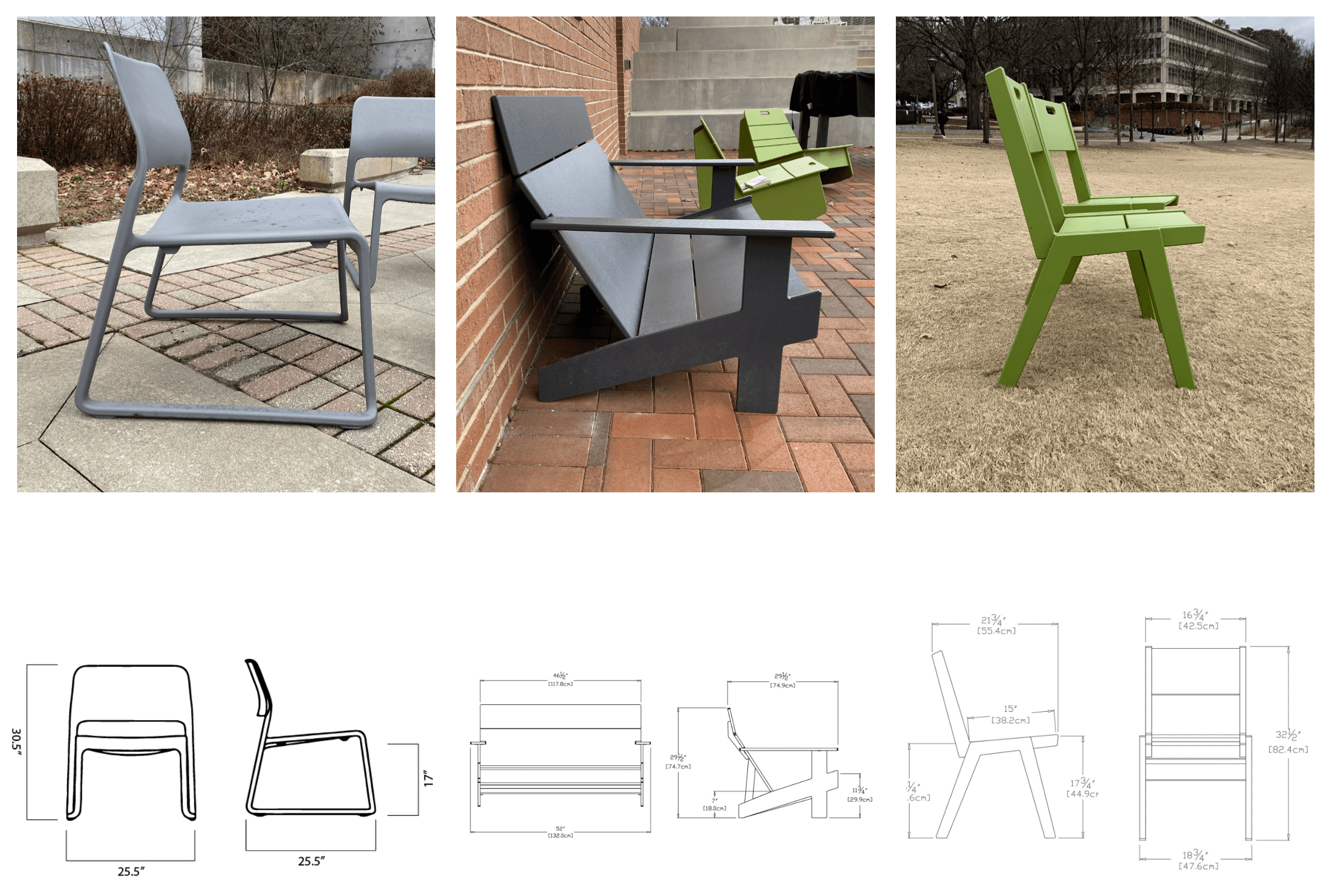
My initial research included lots of market research and extracting the standards of the current dining chair industry. It also included getting used to the idea of different chair measurements and seeing/ feeling them in real life. A small group of pears and I went out and gathered measurements of many 16 different chairs to get a better understanding of the industry.
Design Objectives
So, what am I setting out to create?
1. The design must hold someone up.
2. The design should look cohesive in material and form.
3. The design could be elegantly made from bamboo.
4. The design must utilize tested ergonomic measurements.
5. The design should fit in a modern chic dining display.
6. The design could be eco-friendly.
Ergonomic Testing
What should a dining chair feel like?
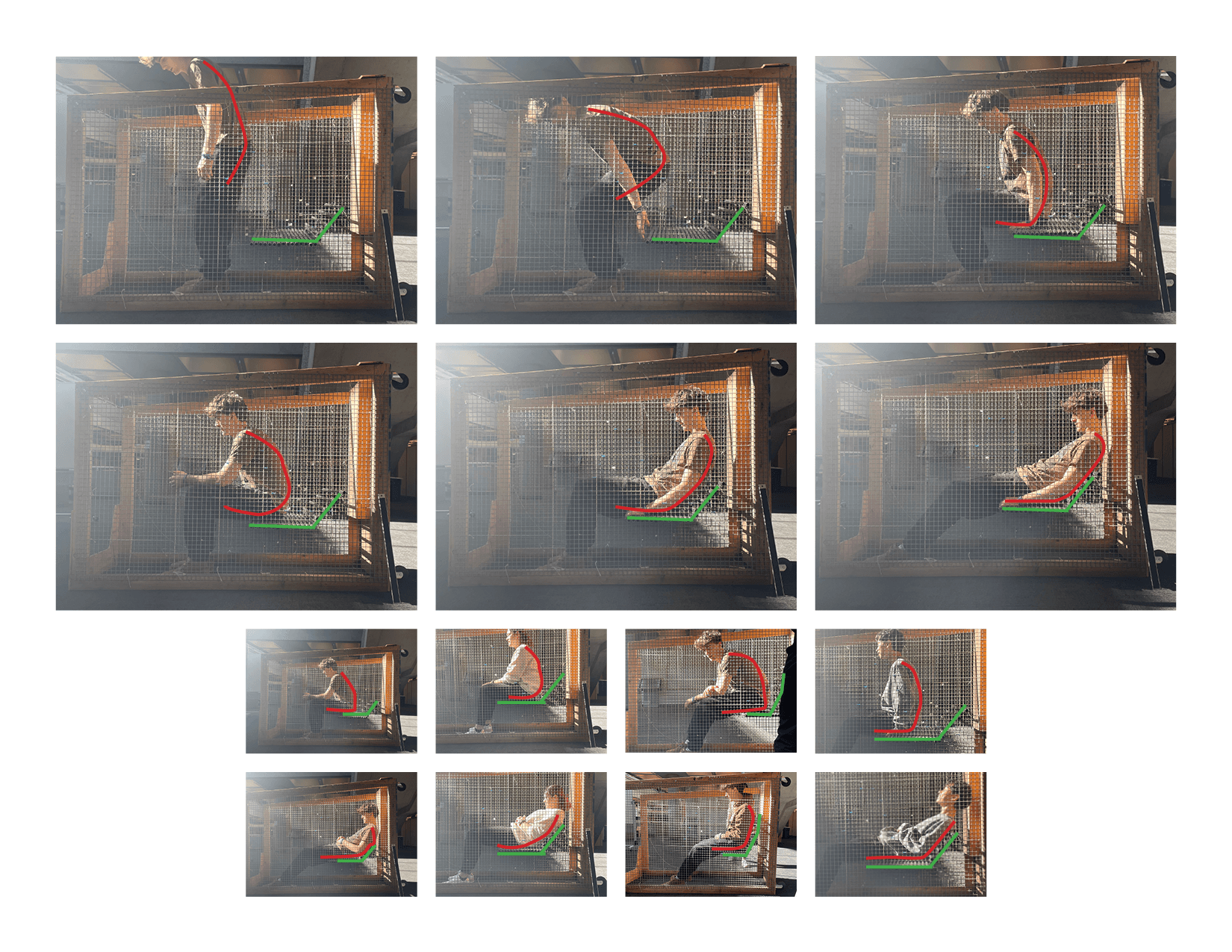
15 +
Ergo-box Test Subjects
30 +
Test variations
19
Analogous Observations
In the process of crafting my chair design, I employed an Ergonomic Test rig unofficially known as the Ergo Box, to systematically evaluate diverse measurements with various test subjects. To ensure precision, a table at the standard height of a kitchen table was integrated to gather authentic feedback for the user's intended activities. Following each test and simulation, I engaged participants in discussions, prompting them to identify pain points and offer suggestions based on their individual body types. This iterative approach allowed me to analyze and synthesize the data, leading to the identification of the most optimal measurements catering to the general population.
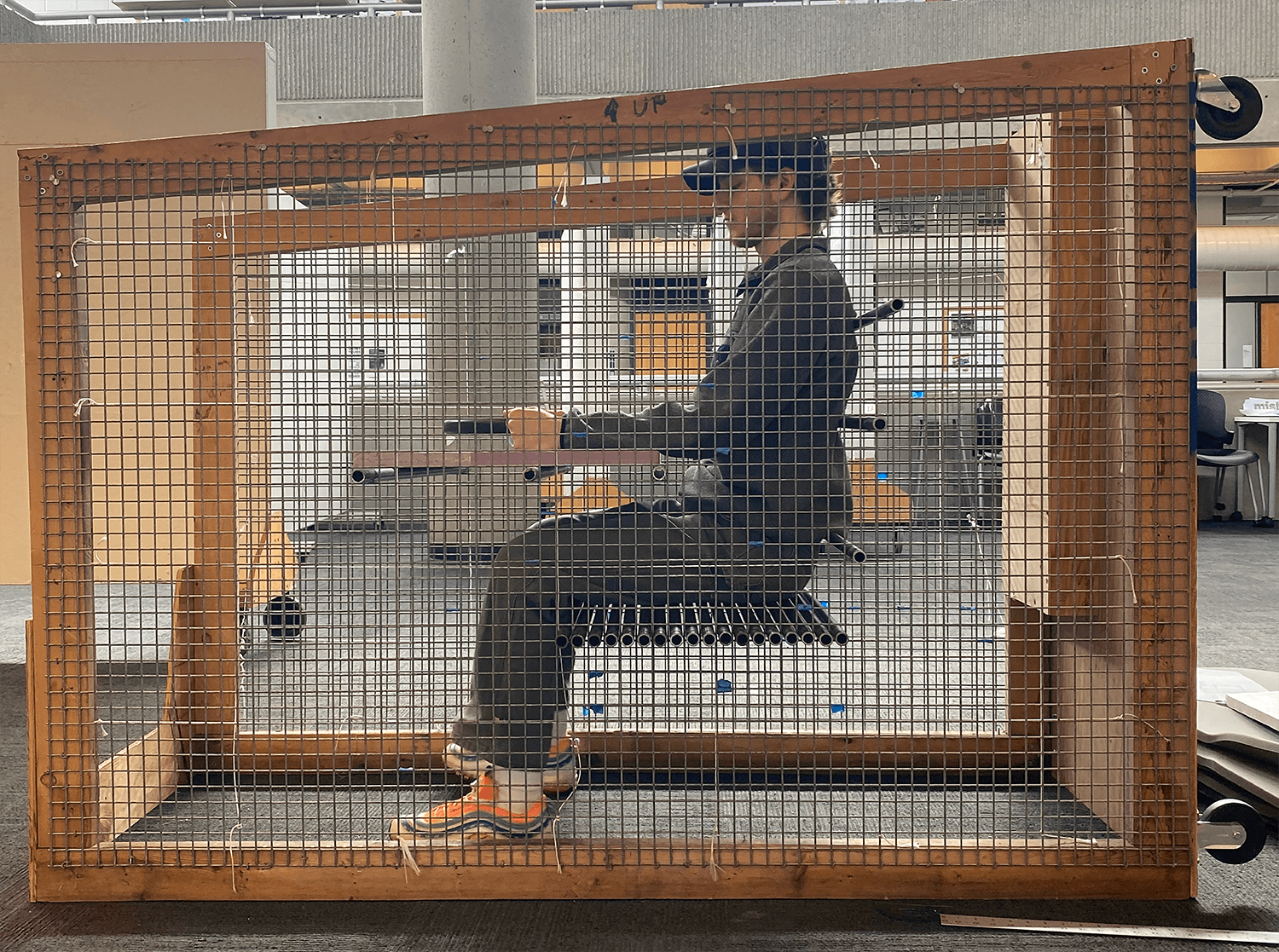
Seat Height
Seat Depth
Seat Width
Back Angle
Back Height
The insights gathered from extensive ergonomic testing guided the final dimensions of the A27 Wahrheit Dining Room Chair. With a seat height of 17.5 inches and a generous seat depth of 18 inches, the chair ensures both comfort and proper support. The back angle at 98 degrees and a back height of 20 inches promote an ergonomic posture, enhancing the overall user experience. Additionally, a thoughtfully designed seat width of 18 inches strikes the perfect balance between snugness and freedom of movement.
Ideation
Envisioning a modern bamboo dining chair and finding inspiration
Throughout my time in design, I have always gravitated toward early Bauhaus work, specifically the home furnishing that came with it. The cantilever chair was first developed by Marcel Brauer and Mart Stam, but traditionally with more conventional materials. I fell in love with the sleek cantilever and committed myself early on to a more ambitious engineering feat.
Another attractive feature of Bauhaus Design is the distinct "Truth To Materials". Walter Gropius, founder of the Bauhaus school, believed materials should be used in the purest and strongest form with limited manipulation and strong natural personalities. Bamboo is one of the world's most distinct and stubborn materials, so Pairing it with manufactured and bent steel could lend to a very pronounced interplay of "Material Truth".
With tubular steel and raw natural bamboo, the concept was prone to adopting a very strong cylindrical design language. I decided to lean into this language with various securing/structural methods, like the steel rounds used in the planking and the filleted leather securing straps.
Material Research
How can this actually be done? Can it?
I originally planned to manipulate the bamboo just as I planned to manipulate the steel, with 90-130-degree bends. Early on, I figured out that bamboo was very particular in its sheer strength and that bending it would be a great challenge. I tried heating it pre-bend in different forms, including steaming, soaking, and using a heat gun. As you can see above, many of these tactics either forced a splintering crack or destroyed the vibrant green color. Overall, bending my materials was a huge engineering problem as I was unfamiliar with the material processes and did not have specialized tools for each material/measurement.
A second iteration of my design incorporated a unique method of bamboo manipulation where I scored the bamboo around 80% of its circumference and then snapped it so that one small piece of the shoot was able to maintain the originally desired visual "bend". Unfortunately, because of time and material limitations, this technique proved to be far too irregular and would snap and fracture down the middle of the bend, so I eventually had to steer away from the literal bend in my final design.
Construction
Meticulous craftsmanship needed to breathe life into the vision.
I was able to bend the 5/8 diameter steel I bought around a Hossfeld Bender in our metal shop. This Bender uses manual force and does not contain any automated bending, so I had to create a very creative and replicable workflow so that both sides of my chair would contain the exact same angles. After bending, I was able to insert square pipes into the connections to add friction and secure a tight fit before welding each touch point.
Once I had all of the pieces cut, bent, and holed, it was time to weld the frame together, Something I had never done before. By welding every joint, I was able to guarantee strong steel connections and a supportive structure for the user. I was also able to use an angle grinder on each connection to maintain the tubular structure of the steel. By strategically placing all of the welds at major connection points on the frame, I was able to cleverly cover up each weld with the leather straps used to secure the bamboo seat bed.
One of my biggest struggles in production was creating the bamboo seat bed and back. the material I was working with was locally sourced by myself from a backyard in Atlanta, so it was extremely irregular and limited. The way I cut each piece left one "node" in the middle of each segment which I was able to sand down and match up with neighboring segments. this allowed me to create continuous strong panels that I eventually predrilled and secured with a steel roll. Drilling these holes into such a natural material made accuracy my biggest priority, eventually securing all 14 shoots with no additional adhesive agent.
The final element of my design was the black leather feet and secure straps. I utilized my studio's laser cutter to cut my strap pattern, guaranteeing perfect replicable measurements and thread pathways for the feet. Each leather strap was tension fit and able to be removed and disassembled at any point, but they also covered each and every weld mark. the feet were sewn with leather thread and used to solidify a sturdy connection with the ground.
Final Design
